Revealing the Ins And Outs of Fasteners and Machining Procedures for Ideal Performance
In the world of design and manufacturing, the choice of bolts and the intricacies of machining processes play a critical function in figuring out the utmost performance and resilience of a product. From the seemingly simple task of selecting the appropriate kind of bolt to the complex accuracy machining strategies employed, every action in this procedure demands meticulous focus to information. As we start this exploration right into the world of bolts and machining, we will discover the refined yet important factors that can significantly affect the performance and quality of the last product, clarifying the frequently ignored aspects that can make all the difference in attaining optimal performance.

Relevance of Correct Fastener Selection
Selecting the appropriate bolts is vital in guaranteeing the structural integrity and durability of any kind of mechanical setting up. Fasteners play a basic role in holding components together securely, with the ideal choice contributing considerably to the total performance and integrity of the assembly. When picking bolts, aspects such as material compatibility, environmental problems, load-bearing capacity, and ease of setup need to be thoroughly taken into consideration to assure optimal efficiency.
Incorrect fastener choice can cause an array of concerns, consisting of loosening, corrosion, and also structural failure. Making use of fasteners that are not matched to the specific demands of the setting up can endanger its capability and present safety risks. Consequently, designers and developers should diligently examine the application requires and pick bolts that satisfy or surpass the essential standards and requirements.
Additionally, the correct bolt selection process includes examining the joint layout, prepared for lots, vibration levels, and prospective thermal growth or contraction to ensure that the picked fasteners can hold up against the operating conditions properly. By focusing on appropriate bolt selection, makers can boost the top quality, toughness, and performance of their mechanical assemblies.
Kinds and Attributes of Fasteners
A necessary element of mechanical assemblies lies in comprehending the diverse types and one-of-a-kind characteristics of fasteners utilized in different industrial applications. Fasteners are vital elements that hold frameworks together, guaranteeing security and capability.
Screws are threaded bolts that are frequently utilized to sign up with 2 or more components with each other. Nuts are internally threaded bolts that mate with bolts to hold parts together. Washing machines are thin plates that distribute the load of a bolt, protecting against damages to the material being attached.
Understanding the qualities of each kind of bolt is crucial for picking the appropriate one for a particular application, ensuring optimal efficiency and integrity of the mechanical assembly. Fasteners and Machining.
Precision Machining Methods for Performance
The intricate design requirements of numerous fasteners browse around these guys necessitate employing precision machining methods for ideal effectiveness in making procedures. One of the primary strategies utilized in precision machining is Computer Numerical Control (CNC) machining, which makes it possible for high degrees of precision and repeatability in the manufacturing of fasteners.
By using accuracy machining strategies, producers can enhance the quality of bolts, minimize product waste, and boost overall production efficiency. The usage of sophisticated machining procedures assists ensure that bolts fulfill industry standards and customer expectations for efficiency and reliability.

Factors Influencing Machining Process Performance
Various variables play a considerable role in determining the efficiency of machining procedures in the manufacturing of fasteners. The initial essential element is the choice of cutting tools. Selecting the appropriate tools based upon the product being machined, desired finish, and cutting rates can greatly impact the performance and top quality of the machining procedure. Additionally, the cutting specifications such as cutting speed, feed price, and deepness of cut are vital variables that influence performance. Fasteners and Machining. Optimizing these criteria based on the particular requirements of the fastener being produced is crucial to achieving cost-effective and accurate machining.
Device rigidness and stability also play an essential duty in identifying machining procedure performance. An educated operator can make real-time modifications, troubleshoot issues successfully, and guarantee that the machining process runs smoothly, ultimately influencing the final high quality of the bolt.
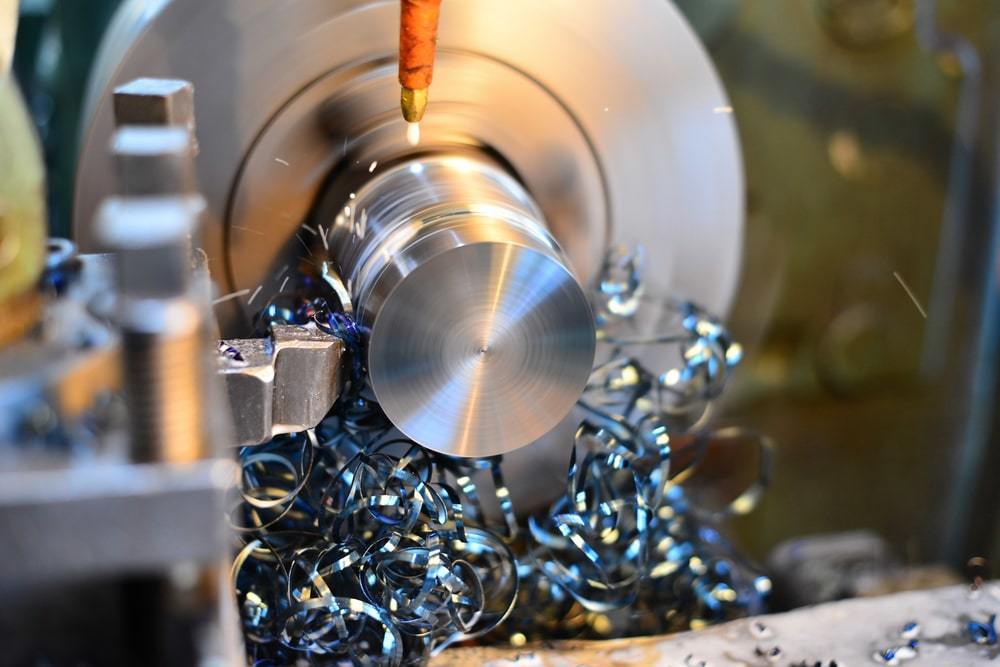
Quality Assurance Steps in Manufacturing
Elements affecting machining procedure efficiency, such as reducing tool choice and equipment security, directly influence the implementation of quality control actions in manufacturing. Regular upkeep of machining tools is likewise vital to maintain high quality control. By adhering to rigid high quality control steps, manufacturers can boost customer contentment, develop a track record for integrity, and ultimately achieve optimum efficiency in their machining procedures.
Final Thought
In verdict, selecting the best fasteners and making use of accuracy machining strategies are necessary for optimal performance in making Continued processes. Recognizing the types and attributes of bolts, along with factors influencing machining procedure performance, can lead to enhanced efficiency and quality assurance procedures. By paying interest to these intricacies, manufacturers can accomplish higher levels of efficiency and integrity in their products.
In the realm of engineering and manufacturing, the choice of bolts and the intricacies of machining procedures play an essential function in figuring out the best efficiency and resilience of a product (Fasteners and Machining). One of the primary methods made use of in precision machining is Computer system Numerical Control (CNC) machining, which allows Get the facts high levels of precision and repeatability in the manufacturing of fasteners. The use of innovative machining procedures helps make sure that bolts meet industry standards and customer expectations for efficiency and reliability
In conclusion, picking the best bolts and making use of precision machining strategies are necessary for optimal efficiency in manufacturing procedures. Recognizing the kinds and characteristics of fasteners, along with variables influencing machining procedure efficiency, can lead to boosted performance and high quality control procedures.
Comments on “The Duty of Fasteners and Machining in High-Quality Item Style”